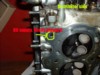 |
This is the oil supply hole. It is necessary to have it plugged. You may opt to have machine shop perform the task or if you are familiar with using a tap, you can do it yourself. Tap the hole with a 1/8NPT tap and plug the hole using a 1/8NPT plug. Be sure to use lock tite prior to screwing it in. If you damage the head, it will need to be resurfaced. Take your time. |
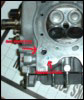 |
Once plugged, this is what it should look like. |
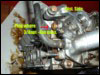 |
This is a plug in the back of the head. Remove this plug and replace it with a 3/8NPT to -4AN fitting. You will run your SS oil line from this location. Be sure to use teflon tape on the threads. |
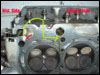 |
There are two places you can relocate the dowel pins. We chose to relocate them to the position shown in the picture. This involves modifying the dowel pin holes on the LS headgasket to match. Keep in mind the holes on the gasket aren't the same size. We recommend using a machine shop to do the work however, if you have experience with a drill press then you can perform the task yourself. Remove the dowel pins from their stock location (which is marked by the red arrows) and reposition them to the space provided. In order for them to fit in their new location, you must mill out that hole to the size of the dowel pin. |
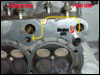 |
Repeat the process on the timing belt side. |
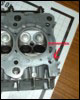 |
The second method to relocate the dowel pins is simpler. On the intake side of the head there are two locations on the left and right that are good for putting the dowel pins. All that is required using this method is that you resize the holes to fit the dowel pins. The LS headgasket already has the correctly sized holes, therefore there is no need to modify the headgasket. |
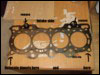 |
Here is a picture of the headgasket. The bottom left and bottom right hand corners are where the dowel pins go if you decided to use the second method. As you can see, the holes on the headgasket don't need to be modified. In some applications, the two brass rings labeled 'REMOVE' on a headgasket need to be removed, otherwise the head will sit on top of those and will not seal. Be absolutely sure you remove the two on the exhaust side only. |
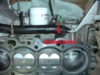 |
Pictured here is the back of a B18a block. Notice there is no knock sensor. The knock sensor came on the 92+ VTEC engines only. If your block doesn't have a knock sensor, you will need to located a hole for one. |
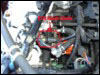 |
Pictured here is the B17 block with the stock location for the knock sensor. |
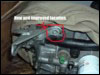 |
On a B18a block we chose to remove one of the mounting bolts for the alternator bracket and use this as the new location for the Knock sensor. |
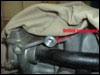 |
Using a 10.9 mm drill bit, opened up the hole on the bracket and the block. Then carefully tap the hole with a 12 mm x 1.25 thread pitch tap. Be sure to clean up the shavings and then screw the knock sensor. This will keep your ECU from throwing any codes. |
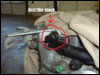 |
Here you can see the knock sensor in its new location. |